DISEÑO DE LAS MEZCLAS
El diseño de las nuevas mezclas se ha llevado a cabo en los laboratorios de ACCIONA Infraestructuras, siguiendo la metodología Marshall. Durante esta fase de diseño,
AIMPLAS realizó la identificación y el acopio de los residuos poliméricos más adecuados para la modificación de las mezclas asfálticas, siguiendo criterios técnicos
(homogeneidad y adecuado comportamiento térmico) y de viabilidad (disponibilidad y coste).
Durante el diseño, se llevó a cabo la fabricación de mezclas asfálticas con porcentajes de 0,5% y 1% de residuos poliméricos de diferente procedencia. Estas mezclas
han sido evaluadas según su resistencia a la deformación, contenido de huecos y sensibilidad al agua. Los resultados obtenidos fueron comparados con una mezcla de
referencia cuya única diferencia con respecto a las mezclas POLYMIX fue la ausencia de residuo polimérico en su composición.
Teniendo en cuenta estos criterios y los resultados obtenidos durante la fase de diseño, los residuos poliméricos que resultaron más adecuados para
la modificación de las mezclas asfálticas fueron los siguientes:
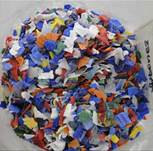 |
|
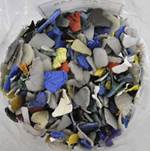 |
Polipropileno procedente de tapones |
|
Polietileno procedente de envases |
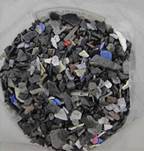 |
|
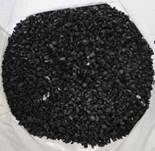 |
Poliestireno procedente de perchas |
|
Caucho procedente de neumáticos fuera de uso |
Las cuatro mezclas resultantes (POLYMIX-PP, POLYMIX-PE, POLYMIX-PS y POLYMIX-NFU) cumplieron los requisitos establecidos en el PG-3 relativos a
la deformación plásticas, sensibilidad al agua y contenido de huecos. Es destacable el aumento en la resistencia a la deformación plástica de
las cuatro mezclas con respecto a la mezcla de referencia.
La caracterización completa de las mezclas, incluyendo la evaluación de la resistencia a la fatiga, módulo resiliente, módulo dinámico, adherencia,
deslizamiento y efecto de la temperatura en el módulo resiliente, se llevará a cabo en el laboratorio de caminos de la Universidad de Cantabria. Los
resultados obtenidos en esta caracterización se compararán con los resultados obtenidos durante la monitorización del tramo piloto.
RESULTADOS DE LA CARACTERIZACIÓN
Las mezclas modificadas con polímeros fueron caracterizadas mediante diferentes ensayos para conocer mejor sus propiedades y el rendimiento de cada polímero.
La caracterización en laboratorio se ha llevado a cabo por el Grupo de Investigación de tecnología de la Construcción (GITECO) en colaboración con el Grupo de Caminos
de Santander (GCS), ambos pertenecientes a la Universidad de Cantabria.
Las muestras fueron fabricadas por ACCIONA Infraestructuras S.A., en sus instalaciones del Centro Tecnológico de I+D+i en Madrid.
De acuerdo a los resultados obtenidos durante la caracterización de las nuevas mezclas POLYMIX (ver siguiente figura), todas las mezclas que incorporan residuos
poliméricos presenten mejor resistencia a la deformación plástica (roderas) que la mezcla de referencia. Así mismo, las mezclas POLYMIX presentaron en general mayor
módulo dinámico, sin comprometer su resistencia a fatiga que se mantuvo en niveles similares a la mezcla de referencia.
ESCALADO DEL PROCESO DE FABRICACIÓN
Tras el diseño de las mezclas, se comenzó el estudio del escalado del proceso de fabricación de las mezclas con adición de polímeros reciclados. Para ello, se visitó
la planta asfáltica de la empresa encargada del extendido del tramo piloto. Durante la visita, se analizaron los procesos y equipos utilizados en la producción de las
mezclas convencionales y se valoraron las posibles modificaciones necesarias para la fabricación de las nuevas mezclas POLYMIX.
El proceso de fabricación de las nuevas mezclas POLYMIX es muy similar al proceso convencional de fabricación de mezclas bituminosas en caliente. La principal diferencia
se encuentra en la fase de tambor mezclador donde mediante un sistema dosificador de aditivos sólidos, se añade el tipo de residuo deseado en función de la mezcla que
se esté fabricando.
Desde el punto de vista de modificaciones necesarias en la planta asfáltica, tan solo la instalación del nuevo sistema dosificador de aditivos es necesario. Es un cambio
menor dentro de la planta asfáltica y de fácil implementación en cualquier empresa del sector.
VIABILIDAD ECONÓMICA
El objetivo de este estudio es valorar desde el punto de vista económico la viabilidad del uso de las nuevas mezclas desarrolladas.
Teniendo en cuenta que la principal diferencia en la fabricación, extendido y compactación de las mezclas POLYMIX con respecto a la de referencia es la adición de los
polímeros, el coste por kilómetro de carretera de estas mezclas será en todos los casos superior al de la mezcla de referencia, debido al sobrecoste de los polímeros
residuales.
Sin embargo, si los resultados positivos obtenidos en el laboratorio son validados, los beneficios de la mejora en las propiedades mecánicas de las mezclas con polímeros
deben valorarse y tenerse en cuenta en el estudio de viabilidad económico.
Los resultados obtenidos en los ensayos dinámicos de todas las mezclas (referencia y mejoradas con polímeros) serán utilizados para estudiar su efecto sobre el comportamiento
estructural del firme con el software Alizé LCPC.
Según los resultados obtenidos con el Alizé, los firmes POLYMIX-PP (incorpora polipropileno) y POLYLMIX-NFU (incorpora neumático fuera de uso) permiten reducir el espesor de
capa necesaria en 2cm, reduciéndose de esta forma las toneladas de mezcla asfáltica necesarias por kilómetro de carretera. La reducción de dos centímetros en el firme compensa
el sobrecoste debido a la adición de los residuos poliméricos a la mezcla, resultando las mezclas viables desde el punto de vista económico.
VALIDACIÓN TÉCNICA
Con el objetivo de validar la tecnología POLYMIX, las cuatro mezclas diseñadas y caracterizadas en el laboratorio fueron implementadas en un tramo real. La ejecución del tramo
experimental dio a conocer problemas que pueden surgir durante una obra real, lo que permitió establecer una serie de recomendaciones para la fabricación y puesta en obra de
las nuevas mezclas POLYMIX.
Los tramos experimentales han sido monitorizados durante 18 meses, siguiendo la evolución de las propiedades estructurales y superficiales de las mezclas y comparándolas con
la mezcla de referencia.
El principal resultado obtenido de la monitorización del tramo experimental es la confirmación de los resultados de laboratorio en cuanto a la mayor resistencia de las mezclas
POLYMIX a las deformaciones plásticas (roderas). Esta mejora impactará positivamente en la durabilidad de las mezclas asfálticas.
Por otra parte, la medida de las propiedades superficiales (resistencia al deslizamiento, macrotextura y regularidad superficial longitudinal y transversal) indicó que no hay
diferencias significativas en la evolución con el tiempo de estos parámetros con respecto a la mezcla de referencia.
Los testigos extraídos del tramo piloto fueron analizados en el laboratorio. Los resultados indican que más de un 80% del Poliestireno que se añade a la mezcla asfáltica se
disuelve en el betún. Como consecuencia, el contenido en betún de la mezcla que incorpora Poliestireno presenta un mayor contenido en betún que el resto. Este hecho sugiere
la posibilidad de que esta mezcla podría fabricarse con una menor cantidad de betún virgen, lo que supondría grandes ahorros económicos y medioambientales.
VALIDACIÓN MEDIOAMBIENTAL
Con el objetivo de estudiar el impacto medioambiental de la tecnología POLYMIX, se ha llevado a cabo una evaluación medioambiental de las mezclas asfálticas mejoradas con residuos
poliméricos y se ha comparado con el impacto ambiental de una mezcla asfáltica convencional.
La identificación y cuantificación del impacto ambiental de los tramos de carretera realizados en el proyecto se ha realizado siguiendo la metodología estandarizada en las normas
ISO 1404027, referente al Análisis de Ciclo de Vida (ACV).
Para llevar a cabo este análisis, se han tenido en cuenta todas las entradas y salidas de los procesos de producción e implementación del tramo piloto ejecutado. Esto incluye, la
producción de las materias primas, suministro de energía, fabricación de productos, servicios de transporte y la implementación (extendido y compactado) de los productos desarrollados.
Los datos necesarios para dichas entradas y salidas proceden en la mayoría de los casos del tramo de demostración ejecutado.
El impacto medioambiental de las mezclas POLYMIX que emplean PP, PS y NFU es inferior al de la mezcla de referencia en todas las categorías de impacto analizadas.
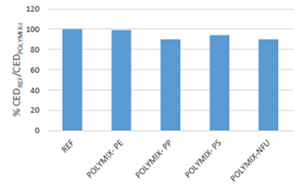 Demanda de Energía Acumulada
|
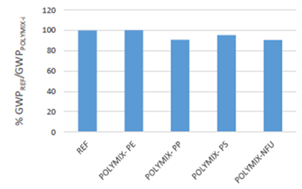 Potencial de Calentamiento Global
|
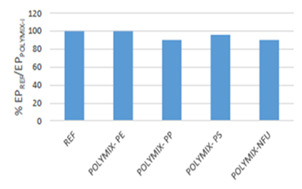 Potencial de Acidificación
|
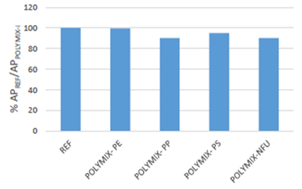 Potencial de Eutrofización
|
OPORTUNIDADES PARA LA REPRODUCIBILIDAD Y LA APLICACIÓN COMERCIAL DE LA TECNOLOGÍA
La aplicación comercial de un nuevo producto o tecnología es un largo camino no exento de obstáculos. Con el objetivo, de definir una estrategia para la futura reproducibilidad
de la tecnología, se ha llevado a cabo la identificación de sus principales amenazas y fortalezas.
Amenazas o barreras:
1) Es necesario mucho tiempo para la estandarización de nuevos desarrollos en el campo de la construcción.
2) Reticencia de la administración a la adquisición de nuevas tecnologías.
3) Existencia de alternativas como el betún modificado con polímeros, actualmente validado y estandarizados de acuerdo a la normativa Europea.
4) Falta de sistemas de recogida y tratamiento de residuos que permitan un flujo constante de polímeros residuales.
En cuanto a las fortalezas y oportunidades, se presentan las principales:
1) Mayor resistencia a la deformación plástica.
2) Alta generación de residuos poliméricos en el mundo.
3) Tecnología fácilmente exportable.
4) Tecnología barata comparada con el betún modificado con polímeros.
5) Incremento de condiciones climáticas adversas y del tráfico pesado en Europa.
6) Nuevas reglas de la contratación pública en Europa que fomenta el empleo de tecnologías más rentables durante su ciclo de vida.
Finalmente, se ha desarrollado una metodología sobre la incorporación de criterios sostenibles en la contratación pública relativa a la construcción de carreteras. Esta guía se
puede descargar
aquí.