DESIGNING OF THE ASPHALT MIXES
For the design of the asphalt mixes, either standard or modified with polymers, the Marshall Methodology has been used. This methodology is based on the volumetric relation of asphalt mix (density-voids content and stability-deformation).
For the characterization of these mixes following tests have been carried out:
- |
Fraction granulometry (PG-3). |
- |
Density (UNE-12697-6). |
- |
Voids content (UNE 12697-8). |
- |
Marshall test. |
- |
Water sensitivity (UNE 12697-12). |
- |
Wheel tracking test (UNE 12697-22). |
During this phase, AIMPLAS identified the most suitable polymeric wastes for the modification of asphalt mixtures. For the selection of the polymeric wastes,
technical and economical aspects have been taking into account, including availability of each waste. The aim of this stage has been focused on the search of
suitable waste materials, thinking in its real application in the road, where big quantities of homogeneous materials are needed.
Polymeric waste was characterized through Differential Scanning Calorimetry. In this technique, the sample is subjected to a controlled temperature program
and differences in energy absorbed or released by the sample with respect to a reference are measured. The information given by this test was essential to predict
polymer performance in the asphalt mixture.
The influence of these wastes was analyzed by characterizing the modified asphalt mixes mechanically and comparing these results with the reference (the same asphalt mixture without adding polymers).
In total, 18 waste materials were selected and tested by AIMPLAS and ACCIONA. Taking into account the following criteria; homogeneity, handling, workability and voids content of all these mixtures,
the final polymeric wastes selected as the most appropriate for this use are the following:
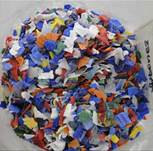 |
|
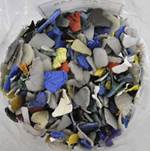 |
Polypropilene from caps |
|
Polyethylene from packs |
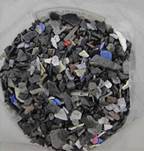 |
|
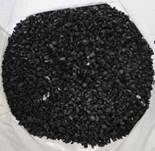 |
Polystirene from hangers |
|
Rubber from end of life tyres |
Taking into account the following criteria; homogeneity, handling, workability and voids content of all these mixtures, a percentage of 1% was finally selected as the optimal percentage for the polymeric waste.
All four mixtures modified with polymers comply with the requirements of PG-3. Moreover, an improvement in the resistance to plastic deformation was found in all of them.
The four POLYMIX mixes and the reference are being characterized at the Roads Laboratory of the University of Cantabria. Results obtained from this characterization
will be compared with the results obtained from the Pilot road monitoring.
CHARACTERIZATION RESULTS
The laboratory characterization was carried out at the facilities of the Research Group in Construction Technology (GITECO) and the Research Group in Roads (GCS), both groups belong to the University of Cantabria.
The samples were manufactured by ACCIONA INFRAESTRUCTURAS, S.A., using their facilities at the R+D+I Technology Centre in Madrid.
According to the results obtained during the design and characterization of the new mixes (see figure below), all of them met the technical requirements currently set out in the Spanish normative for their use in road
construction both as wearing and base course. In addition, compared to the reference, all asphalt mixes that incorporate polymer waste present better resistance to plastic deformation and higher dynamic modulus without
compromising its fatigue resilience.
UP-SCALING OF THE PRODUCTION PROCESS
Since the asphalt mixes modified with recycled polymers are new and innovative products, previous to the implementation stage it was necessary to analyse the processes
and equipment used in regular asphalt mixes production, and evaluate what changes or modifications were needed to the manufacture of the new mixes. The defined production
process was successfully validated by testing a small batch produced at the asphalt plant.
Main conclusion obtained from this study was the feasibility of POLYMIX mixes to be produced in virtually any asphalt plant by simply incorporating a dosage system for the addition of the polymeric waste in to the drum.
ECONOMIC FEASIBILITY OF POLYMIX TECHNOLOGY
The economic feasibility was checked by analysing the construction costs of the new mixes and comparing these costs with conventional asphalt mixes. POLYMIX mixes were
found to be more expensive than conventional mixes due to the higher cost of polymer waste as regards to natural aggregates. However, due to the better performance of
POLYMIX mixes, the possibility to reduce the thickness of the asphalt layer was studied with Alizé LCPC. Polymer modified asphalt mixes that incorporated polypropylene
or rubber from ELT were found to be more cost-effective than conventional mixes. Polystyrene modified asphalt mixture was just a bit more expensive.
TECHNICAL VALIDATION
In order to demonstrate the technical feasibility of the technology, the four mixes designed and characterized at the laboratory were successfully implemented at a real
scale road and their performance assessed during 18 months. The evolution of the surface and structural properties of the mixes were evaluated and compared with the
reference.
Main result obtained from the monitoring activity is the confirmation, in agreement with the laboratory results, of the higher resistance of POLYMIX asphalt mixes to
rutting. This will likely positively impact on the durability of the asphalt mixture.
On the other hand, road surface properties such as the skid resistance, the macrotexture and the longitudinal and transverse surface regularity were measured during
the monitoring of the road. In general, no significant variations between the mixtures were found. All sections, including the reference, had a similar behaviour and
therefore such variations are not dependent of the addition of polymer waste to the asphalt mixture.
From the characterization of core samples extracted from the pilot road, it could be observed that from the four polymers studied, only polystyrene dissolved in more
than 80% in bitumen. As a consequence an excess of bitumen in the asphalt mixture was found, so that the possibility to reduce the amount of virgin bitumen in the
asphalt mixture is expected. If this is confirmed, the cost of this mixture would be significantly reduced.
ENVIRONMENTAL VALIDATION
Finally, the potential environmental impact of the technology was evaluated. This assessment was carried out through a Life Cycle Assessment following the methodology
recommended by the International standard ISO 14040-43. All input and output values for the individual processes in the production and on-site implementation of the
asphalt mixes were taken into account.
Comparison of the environmental impact of the different asphalt mixes developed shows that, on the 4 category impact analyzed, POLYMIX mixtures present slightly
better environmental performance. Therefore, the reuse and exploitation of plastic waste in bituminous mixes not only does not increase the environmental impact of
the final product, but in some cases it is even reduced.
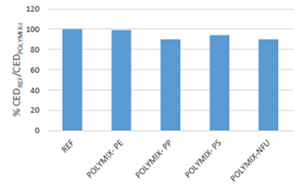 Cumulative Energy Demand
|
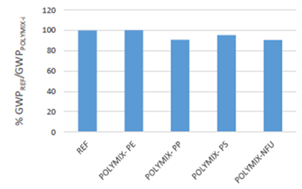 Global Warming Potential
|
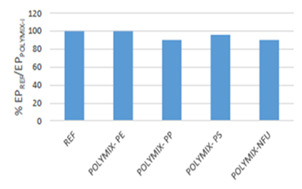 Acidification Potential
|
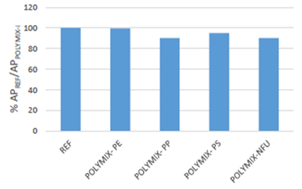 Eutrophication Potential
|
POTENTIAL FOR REPLICABILITY AND COMMERCIAL APPLICATION
In order to give a clear idea of the potential for the replicability and commercial application of the technology, main threats and drivers of POLYMIX technology were identified.
On the one hand, main threats for the quick uptake of the technology are:1) the long time needed for the inclusion in regulations of new developments, 2) the reluctance of Road
Authorities to the uptake of new innovations that are not regulated, 3) the existence of other solutions such as Polymer Modified Bitumen, already validated and included in EU
normative and accepted by Road Authorities and 4) the low availability of recycled waste plastic streams due to the lack of collection schemes.
On the other hand, regarding main drives of POLYIMIX technology are: 1) Better rutting resistance of these mixes comparing to conventional mixes, 2) high consumption rate of
polymers worldwide, 3) easy exportable technology, 4) cheap technology comparting to Polymer Modified Bitumen, 5) the increase of freight traffic and harsh climatic conditions
in EU have increased the need of more resilient asphalt mixes and 6) new EU public procurement rules encourages the evaluation of tenders based on cost-effectiveness.
Finally, a methodology was developed to provide information about the technical specifications and requirements that could be included in Green Public Procurement processes to
boost the use of eco-friendly asphalt mixes. Although the methodology was developed on the basis of the Spanish scenario, the adaptation to other European countries was also
analyzed. A case study with POLYMIX technology is presented in the guideline “Green Public Procurement. Polymix guide”. This guideline can be downloaded
here.